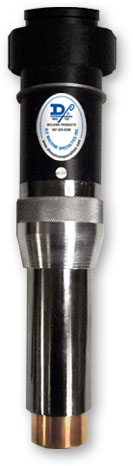
W/C Twin Machine Barrel
Drawings Accessories More Info
Overview
To provide maximum resistance to the abuses of day to day service, the D/F Twin MIG torch is of heavy duty construction with all metal parts well insulated from current carrying members. The compact in-line body allows the D/F Twin MIG Torch to be used in a variety of applications with ease of maneuverability and can access hard to reach areas of operation. To facilitate reparability, all service lines are externally connected to the torch body and exit from the rear of the torch barrel. The torch can use either threaded contact tips or slip-in contact tubes which are secured with a collet nut supplied with the torch. The contact tip can be quickly and easily replaced by unscrewing the metal nozzle and collet nut, and removing the tip. The D/F Twin MIG Torch like all D/F torches is easily reparable, thus reducing downtime and increasing productivity.
The Twin Wire 1200 amp high current machine torch is recommended for robotic welding applications where production demands the maximum durability and quality for robotic gas metal arc welding. The D/F Twin Wire 1200 amp high current machine torch is not a Tandem torch. It is a true twin wire torch (two wires used with one power source). The Twin Wire 1200 Amp as provided will accommodate two 1/8" CrZr - (Cr-Chromium Zr-Zirconium) threaded current tips. The water-cooled nozzle accepts threaded gas nozzles. This barrel is primarily for wire diameters from .045" thru 1/8" (1.143mm thru 3.175mm). The suggested current level with the threaded gas nozzles with the Twin 1200 Amp would be approximately 750 amperes (depending on application). Maximum current capacity applicable to all models is 1200 amperes.
The D/F torch is famous for the fact, that if it is chilled properly, the welder can grab the chrome front water-cooled barrel (not the copper gas nozzle/cup) of the torch with their bare hand and it will be cold to the touch seconds after welding. With the proper chiller, this can be done even after a 4 hour arc time. Make certain the cooling water supply is at least the minimum flow rate of 1 gallon per minute (for each inner body), at 40 psi (80 psi maximum) with a 6 gallon reservoir and a recommended 30,000 BTU/hr cooling capacity. Gun ratings are affected by shielding gas used, arc time, cooling time and inlet water temperature. Water outlet temperature should not exceed 27°C (80°F). The torch’s water out & power cable is not cooled until the coolant has gone through the torch and out the water out & power cable. If water is not flowing through the D/F torch for at least 1 minute prior to striking an arc, when you apply the power and water hits the “hot” water/out & power cable, you will generate steam. Steam can damage the torches internals in seconds causing a leak. It can also blow out the torches water/out & power cable. A flow switch can be installed after the return line ensuring that coolant is present at the return line prior to striking an arc. When High-Deposition GMAW, high current density, high amperages, preheat, or extended periods of arc time are used, a refrigerated liquid chiller with a larger reservoir is required. Precise temperature control maintains the cooling at a constant 13°C (55°F) temperature, thus prolonging the life of the welding equipment and more specifically extending the service life of the gas nozzle and current tip.. D/F Machine Specialties does not manufacture or sell chillers, we only recommend them. Click here to see our recommended chillers.
Each D/F Machine Specialties welding gun is fully assembled and ready to install. In order to make the installation complete, the code number, wire size, wire feeder make/model (Lincoln wire feeders, Miller wire feeders, Tweco wire feeders, ESAB wire feeders, & EURO Quick Disconnect wire feeders), and inlet (as needed) must be specified when ordering. If special welding tools or accessories other than those listed previously are required, please consult with the factory. Get the right feeder adapter connection to fit your MIG wire feeder.
Features
- 1200 Amps Continuous Duty Cycle
- Two (2) Current Tips for Very High Deposition
- Water-Cooled Inner Bodies & Nozzle
- Large Frontal Area for Increased Gas Coverage
- Small Frontal Tapered Nozzle for Single Wire Applications
- Withstands Preheat & Extreme Conditions
- Adaptable to Any Wire Feeder or Power Source
Model Explanation
- NCM-TDP - Normal Duty, Collet Action (Slip-in Tip), Machine Barrel - Twin Dual Power Cables
- HTM-TDP - Heavy Duty, Threaded Tip, Machine Barrel - Twin Dual Power Cables
Model Specifications
MODEL | CURRENT CAPACITY |
WEIGHT (APPROX.) | COOLING REQUIRED | RECOMMENDED WIRE DIA. RANGE |
INSTRUCTION MANUAL |
---|---|---|---|---|---|
NCM-TDP, HTM-TDP | 1200 amps | 20 lbs | 6 quarts/min* | .035"-1/8" (.9m-3.2mm) | 1019 |
*Based on 3 quarts/min for each of the 2 inner bodies |
Barrel Dimensions
MODEL | LENGTH | BODY DIAMETER |
---|---|---|
NCM-TDP, HTM-TDP | 14.5" | 2.750" |
Ordering Information
Complete Barrel Only
DESCRIPTION | CODE NO. |
---|---|
NCM-TDP Tandem W/C Machine Barrel | 41300 |
HTM-TDP Tandem W/C Machine Barrel | 41301 |
Complete Assemblies
DESCRIPTION | CODE NO. | |||||||
4 Ft. | 5 Ft. | 6 Ft. | 7 Ft. | 8 Ft. | 10 Ft. | 12 Ft. | 15 Ft. | |
NCM-TDP | 44705-4 | 44705-5 | 44705-6 | 44705-7 | 44705-8 | 44705-10 | 44705-12 | 44705-15 |
HTM-TDP | 44706-4 | 44706-5 | 44706-6 | 44706-7 | 44706-8 | 44706-10 | 44706-12 | 44706-15 |
Manuals & Downloads
Instruction Manuals
TORCH MODELS | DOWNLOAD |
---|---|
NCM-TDP, HTM-TDP | 1019 Tandem |
CAD Files & Drawings
TORCH MODELS | CODE NO. | CAD FILE | PDF DRAWING |
---|---|---|---|
HTM-TDP | 41301 | 41301 | 41301 |
Other Documents
DESCRIPTION | DOWNLOAD |
---|---|
Torch Connection Options | |
W/C Twin Wire Machine Barrel One-Sheet |
Utility Station #45188 - Dual Power Cable
The D/F Utility Station is required for all D/F torch installations. Typical modern torch setups utilize a unitized cable assembly with a power pin. D/F torches take an alternative approach to the setup. The torches use a separate gas hose, water-in hose, Water Out & Power Cable, and casing/conduit. When one cable goes bad it is simply replaced instead of attaching an entire new unitized cable assembly; a huge cost saver! This is also where the D/F Utility Station comes into play. The gas hose, water-in hose, and Water Out & Power Cables are interfaced with the customer's existing lines via the Utility Station. The D/F torch leads plug into the front (see right) of the Utility Station. Into the back (see below) of the Utility Station go the customer's utilities. Read more on the D/F Utility Station product page.
For more information on proper use of the D/F Utility Station, and to see the various torch connection options, please download the Torch Connection Options one-sheet.
More Info
Twin wire welding is recognized by the American Welding Society (AWS) as parallel wire that uses two wires but only a single power source and typically a single or dual contact tips. It can increase deposition rates by 20 to 30 percent versus single wire welding without significantly increasing heat input. The increase comes from the greater current density achieved by pushing a similar current over smaller, cross-sectional areas of wire.
Twin wire welding offers excellent penetration as the current density is directed axially along each wire. Wires can be aligned in the direction of travel for high travel speeds or oriented perpendicularly to the direction of travel to achieve a wider bead profile.
When twin wire welding, you must use a heavy-duty water-cooled contact assembly. A good contact assembly comprises heavy-duty CrZr (Cr-Chromium Zr-Zirconium) contact tips or a single contact tip with slots for both wires.